Table Of Content
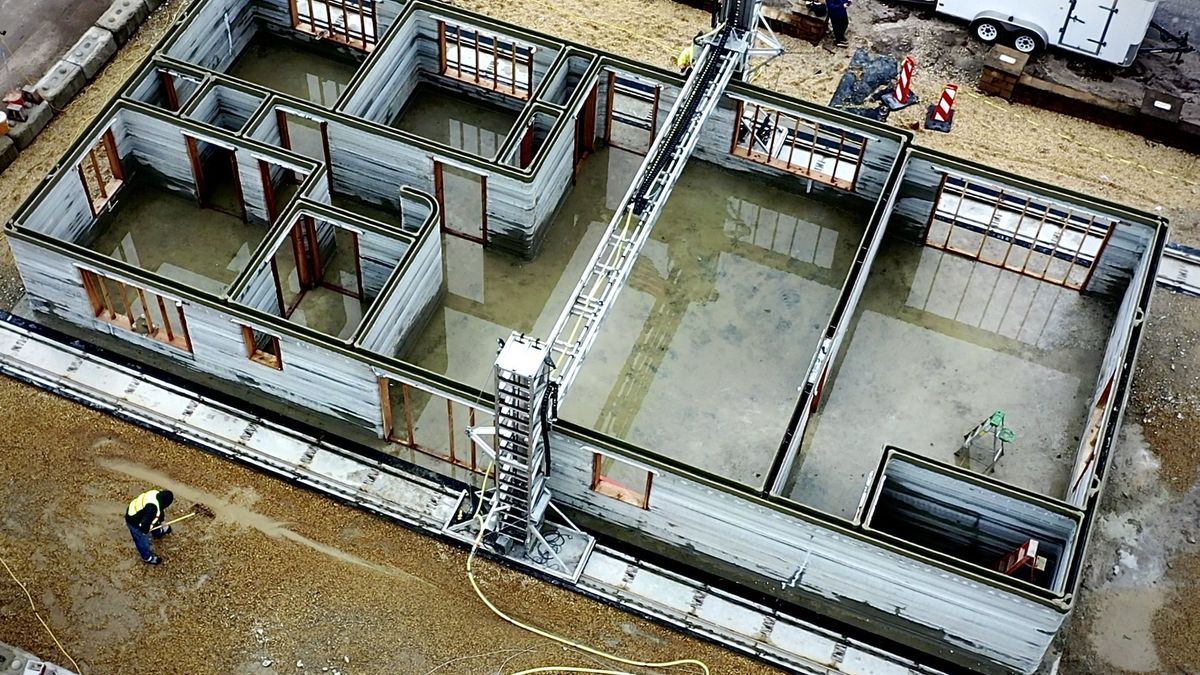
The cost of a 3D printed tiny house also depends on whether or not you factor the cost of the industrial printer or specialized builder into the overall cost. With advancements in technology and materials, 3D printing could revolutionize the construction industry and housing market. The potential for 3D printed houses to address global housing crises is significant, and this technology could help provide affordable and sustainable housing to people in need. While 3D printing technology has come a long way in recent years, it is still in its infancy when it comes to building houses. The size of the printer limits the size of the house that can be printed, and printing a multi-story building is currently not feasible.
Material Options For 3D Tiny Houses
Muscatine tears down first 3D-printed home, planning to try again - WQAD Moline
Muscatine tears down first 3D-printed home, planning to try again.
Posted: Mon, 20 Nov 2023 08:00:00 GMT [source]
According to a report by Yahoo Finance, 3D printed houses can cost as low as $10,000, making them an affordable housing option for many people. Additionally, 3D printed houses can be built in a matter of days, significantly reducing the cost of labor. This affordability makes 3D printed houses accessible to people who may not have been able to afford traditional housing options.
Lack of Skilled Labor
For example, some 3D printed houses are built using concrete, while others are built using a combination of materials such as wood and plastic. 3D printed houses bring the benefits of additive manufacturing to the construction space. The material costs incurred by construction 3D printing are usually an order of a magnitude less when compared to conventional methods. This is while we take into account the fact that 3D printing concrete tends to be more expensive than normal construction concrete. Three-dimensional-printed houses are structures that are built layer by layer using an industrial-grade, 3D-printing technology.
What flooring options work with a passive solar design?
Dagher said there's a shortage of both affordable housing and workers to build homes. The university wants to show how homes can be constructed nearly entirely by a printer with a lower carbon footprint. Concrete 3D printing saves time, uses less material, and requires less manual labor.

Not only was I curious about what a 3D printed tiny house was, I also had tons of questions about the way they’re manufactured, how much they cost, whether or not they’re legal, and more. While 3D printing technology can create structures with high accuracy, there is still a risk of errors and defects. Builders must take extra care to ensure that the printed structure meets safety standards and is structurally sound. Traditional construction methods require a lot of manual labor, which can be time-consuming and expensive. 3D printing, on the other hand, can significantly reduce the amount of labor required, which can lead to significant cost savings.
Why 3D-printed houses could be the future
The machine revealed Tuesday at the University of Maine is four times larger than the first one — commissioned less than five years ago — and capable of printing ever mightier objects. That includes scaling up its 3D-printed home technology using bio-based materials to eventually demonstrate how printed neighborhoods can offer an avenue to affordable housing to address homelessness in the region. Many other companies have been involved in space-building projects, including the European Space Agency and Elon Musk’s SpaceX.
House 3D printers available for sale
Additionally, 3D printing can reduce the amount of waste generated during the construction process, which can also help save money. It’s important to note that the cost of 3D printing a house can vary depending on the location where the house will be built. This is because the cost of materials and labor can vary significantly from one location to another. The materials used for 3D printing a house can also affect the overall cost of the project. The cost of the materials can vary depending on the type of material used, as well as the quality and quantity required. For example, using a high-quality concrete material may result in a higher cost, but it may also result in a more durable and long-lasting structure.
The materials used to build a 3D printed house can also have a significant impact on the overall cost. While some materials may be cheaper than others, they may not be as durable or long-lasting. On the other hand, more expensive materials may be more durable and long-lasting, but they can significantly increase the cost of the project. The company based out of Austin Texas has been awarded the first commercial permit to build a 3D printed house that can appraised and sold in the U.S. Another potential website to check out is However, they are currently only taking requests and not orders.
3D printing could be construction industry paradigm shift 60 Minutes - CBS News
3D printing could be construction industry paradigm shift 60 Minutes.
Posted: Sun, 08 Oct 2023 07:00:00 GMT [source]
The roof, plumbing and electrical wiring are added through more conventional methods by tradespeople. That’s a big “if,” but we don’t want to write off any attempt to tackle Detroit’s housing affordability problem, even when the fix seems far off. She’s excited to see more Ohio companies, like Sustainable Concrete Innovations, investing in the process. The open-plan spaces further have a neutral muted palette with wood cabinetry, woven rugs and touches of greenery.
In fact, in 2019, the first 3D printed house in the United States was completed in Austin, Texas. House 3D printers therefore do not replace people, but complement them; doing the heavy lifting while the specialists do what they do best. It is important therefore to focus on how 3D printed houses can benefit both us and those in the third-world, and respect the advantages that 3D printed houses offer. In poorer areas with few skills builders and little building material available, large house printers such as those by ICON and New Story offer a fantastic way to build basic huts and 3D printed shelters. If able to use locally source material, this reduces building costs dramatically, allowing for shelters to be built for those who need them most.
If you hear of an exciting or innovative building project, there is a high likelihood it will involve Dubai. Dubai have been championing ambitious architectural projects for years, and have recently made the bold move of aiming to have 25% of new buildings 3D printed by 2030. With 3D printed housing specifically, it’s not yet possible to DIY this project. While this may become possible in the future, it should be left in the hands of the experts for now. I want to reiterate here the importance of refraining from building a 3D printed tiny home on your own. I tend to tell my friends that DIY building is for anyone, and you don’t have to have a ton of experience to be successful.
This can help reduce the carbon footprint of construction and make it more sustainable. The complexity of the design is another factor that can impact the cost of 3D printing a house. A more complex design will require more time and effort to print, as well as more materials. Furthermore, the use of 3D printing could revolutionize the housing market by making it easier to provide affordable housing to people in need.
The Winsun 3D printer is a house 3D printer that was in the spotlight a few years ago. In 2015, however, Contour Crafting’s CEO accused Winsun of stealing their patented technology. This easy-to-move house 3D printer is capable of reaching up to 2.75 meters high and requires only two people to operate it. The tradespeople who weren’t answering calls from Citizens Robotics may have had an issue with the very idea of 3D-printed housing. Cost is what’s fueling the hype train, even as fans of 3D printing see many more benefits — from new design possibilities to reduced environmental impact.
No comments:
Post a Comment